Hay varias variaciones de los procesos de moldeo por inyección, muchos de los cuales aún están en desarrollo. Además, debido a la naturaleza diversificada de estos procesos especiales de moldeo por inyección, no existe un método único para categorizarlos. Los procesos especiales de moldeo por inyección más comunes son el moldeo por inyección de varios componentes, el moldeo por coinyección, el moldeo por inyección asistido por gas, el moldeo por inyección-compresión, el moldeo por inyección de reacción y el moldeo por inyección de caucho de silicona líquida.
Moldeo por inyección de múltiples componentes
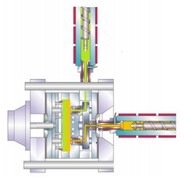
El moldeo por inyección de múltiples componentes (o multicolor) se utiliza para inyectar dos o más componentes a través de diferentes corredores y compuertas. sistemas en diferentes etapas durante el proceso de moldeo. Cada componente se inyecta utilizando su propia unidad de plastificación. Los moldes suelen estar situados sobre una mesa giratoria. Las luces de freno automotrices multicolores se moldean de esta manera. En los procesos de múltiples componentes, a menudo se moldean dos materiales incompatibles o un componente se enfría lo suficiente para que los dos componentes no se adhieran entre sí. Por ejemplo, para moldear un sistema de bola y casquillo, primero se moldea la bola o el casquillo del varillaje. El componente que se inyecta primero se deja enfriar un poco antes de que se moldee el segundo componente. Esto da como resultado un sistema perfectamente móvil; si se inyecta primero el encaje, el conjunto quedará suelto y si primero se moldea la bola, el conjunto quedará ajustado, ya que el encaje se encoge sobre la bola. Este tipo de proceso de moldeo por inyección se usa para reemplazar las tediosas tareas de ensamblaje y se está volviendo popular en países donde los costos de mano de obra son altos. Por lo tanto, este tipo de proceso se denomina moldeo por inyección de ensamblaje. Un método de uso común de moldeo por inyección de componentes múltiples emplea un molde giratorio y varias unidades de inyección. Una vez que se moldea el inserto, un servomotor hidráulico o eléctrico gira el núcleo y la pieza 180 grados (o 120 grados para una pieza de tres disparos), lo que permite inyectar polímeros alternos. Este es el método más rápido y común porque se pueden moldear dos o más piezas en cada ciclo. Otra variación del moldeo por inyección de múltiples componentes implica la expansión automática de la geometría de la cavidad original utilizando núcleos o correderas retráctiles (móviles) mientras el inserto aún está en el molde. Este proceso se denomina extracción del núcleo o recuperación del núcleo. Para ser específicos, el núcleo se retrae después de que el inserto se haya solidificado para crear un volumen abierto que será llenado por el segundo material dentro del mismo molde.
Moldeo por co-inyección
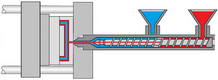
A diferencia del moldeo por inyección de varios colores o de varios componentes, el moldeo por co-inyección utiliza el mismo sistema de entrada y canal. Aquí, primero se inyecta el componente que formará la capa exterior de la pieza, seguido del componente central. Esto se logra con el uso de una máquina que tiene dos unidades de inyección separadas, controlables individualmente y un bloque común de boquillas de inyección con un cabezal de conmutación. Debido al comportamiento de flujo del polímero fundido y la solidificación del material de la piel, una capa congelada de polímero comienza a crecer desde las paredes más frías del molde. El polímero que fluye en el centro de la cavidad permanece fundido. A medida que se inyecta el material del núcleo, fluye dentro de las capas de piel congelada, empujando el material de piel fundido en el núcleo caliente hacia los extremos de la cavidad. Debido al efecto de flujo de fuente en el frente de fusión que avanza, el material de piel en el frente de fusión aparecerá en la región adyacente a las paredes del molde. Este proceso continúa hasta que la cavidad está casi llena y aparece material de piel en la superficie y el extremo de la pieza. Finalmente, se vuelve a inyectar una pequeña cantidad adicional de material de revestimiento para purgar el material del núcleo del bebedero de modo que no aparezca en la superficie de la pieza en la próxima inyección. Cuando no se inyecta suficiente material de revestimiento antes de la inyección de material del núcleo, el material de revestimiento a veces puede agotarse durante el proceso de llenado y el material del núcleo aparecerá en partes de la superficie y en el extremo de la parte que se llenó por última vez. Esto se conoce como superficie del núcleo o avance del núcleo. Existen otras variaciones del proceso de moldeo por coinyección secuencial (a saber, piel-núcleo-piel o A-B-A). En particular, se puede comenzar a inyectar el material del núcleo mientras se inyecta el material de la piel (es decir, A-AB-B-A).
Es decir, la mayor parte del material de la piel se inyecta en una cavidad, seguido de una combinación de materiales de la piel y del núcleo que fluyen hacia la misma cavidad, y luego sigue el resto del material del núcleo para llenar la cavidad. Nuevamente, una pequeña cantidad adicional de inyección en la piel cerrará el final de la secuencia, como se describió anteriormente. Además de la configuración de la técnica de un canal, se han desarrollado técnicas de dos y tres canales que usan boquillas con canales de flujo concéntricos para permitir la inyección simultánea de materiales de piel y núcleo.
El proceso de moldeo por inyección asistido por gas (GAIM) comienza con una inyección parcial o casi total de polímero fundido en la cavidad del molde, seguido de la inyección de un gas inerte (típicamente nitrógeno) en el núcleo del molde. el polímero se derrite a través de la boquilla, el bebedero, el corredor o directamente en la cavidad. El gas comprimido toma el camino de menor resistencia, fluyendo hacia el frente de fusión, donde la presión es más baja. Como resultado, el gas penetra y ahueca una red de canales de gas de sección gruesa prediseñados, desplazando el polímero fundido en el núcleo caliente para llenar y empaquetar toda la cavidad. La inyección asistida por gas, así como otras tecnologías de moldeo por inyección asistida por fluidos, funcionan según varias variaciones de dos principios. El primer principio se basa en llenar parcialmente la cavidad de un molde y completar el llenado del molde desplazando la masa fundida con un fluido a presión. Con el segundo principio, la cavidad se llena casi o por completo y el núcleo fundido se evacua a una cavidad secundaria. Esta cavidad secundaria puede ser una cavidad lateral que se desguazará después del desmoldeo, una cavidad lateral que dará como resultado una pieza real o la cavidad fundida frente al tornillo en la unidad de plastificación de la máquina de moldeo por inyección. En este último, la masa fundida se reutiliza en el siguiente ciclo de moldeo. En el llamado proceso de control de presión de gas, el gas comprimido se inyecta con un perfil de presión de gas regulado, ya sea constante, en rampa o escalonado. En el proceso de control de volumen de gas, el gas se dosifica inicialmente en un cilindro de compresión a un volumen y una presión predeterminados; luego, se inyecta bajo la presión generada por la reducción del volumen de gas por el movimiento del émbolo. Las máquinas de moldeo por inyección convencionales con control preciso del volumen de inyección se pueden adaptar para el moldeo por inyección asistido por gas con un equipo de conversión adicional, una fuente de gas y un dispositivo de control para la inyección de gas. Sin embargo, el moldeo por inyección asistido por gas requiere un enfoque diferente para el diseño de productos, herramientas y procesos debido a la necesidad de controlar la inyección de gas adicional y la disposición y el tamaño de los canales de gas para guiar la penetración del gas de una manera deseable. El proceso de moldeo por inyección asistido por gas es una forma especial de una categoría más general de moldeo por inyección asistido por fluido. Otro proceso que cae dentro de esta categoría es el moldeo por inyección asistido por agua. La principal diferencia de este último proceso es que el agua es incompresible y tiene una conductividad térmica y una capacidad calorífica mucho más altas que el aire. En consecuencia, esto conduce a reducciones significativas en el tiempo de ciclo.